One key transformation driver impacting the Food & Beverage industry is the vision of a digitalized plant, often referred to as “the smart factory” and directly linked with Industry 4.0 and IIoT concepts. The danger in this vision is for digitalization to be seen as a goal in itself. When this happens, the focus on return on investment may be lost. Our experience shows that the optimal situation happens when digitalization clearly serves a business purpose – whether that be innovation in all its forms or sustainability targets.
In an interview published by the website Control Global in November 2021, Charles Tisdell, Global director of automation connected IIoT at AB-InBev said: “Digital transformation is all about people transformation, too, and identifying gaps in data and equipment performance that need to be closed.”
The following video recorded in fall 2021, shows you a real story about how to make the best use of plant floor data, step by step. You can see why the combination of agile project management and the zenon software platform acts as a decisive success factor.
What we can learn from this best-practice example
Let’s reflect for a moment on the story in this film – from its beginning to the perspectives it opens for future. What are your thoughts? Is this all about one single project managed properly that enabled one big step to climb the transformation mountain? Or can we rather observe the agile project management that delivered repeated iterations one after the other? Each step required clear targets, transparent ways to implement the project, and identified roles for the right stakeholders. Every milestone brought proven return on investment enabled by the software platform’s capabilities.
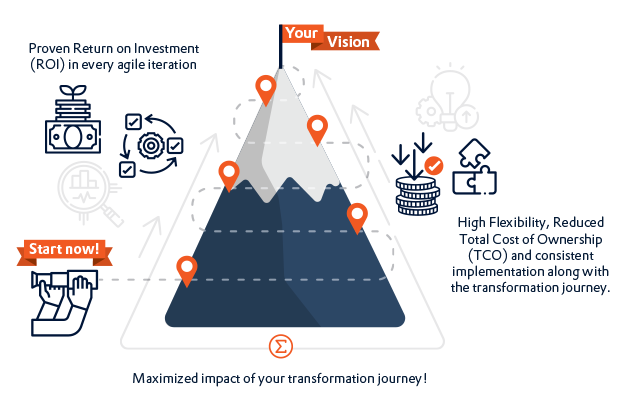
The project team followed a consistent learning path in leading the implementation, as the requirements and as the scope changed along the transformation journey. The key element of using the zenon software platform was to continuously and flexibly fulfil these demands while remaining consistent with the overall vision: operational excellence, transforming plant floor data into robust quality metrics, and ensuring an integrated and well-functioning OT / IT landscape.
Why does the chosen technology impact your transformation journey?
Our example of plant digitalization emphasizes the importance of properly designing the path towards achieving the vision. Successfully reaching a clear return on investment at every step will deliver more when paired with a low total cost of ownership along the entire digitalization journey. The technology you choose can, therefore, limit or help you throughout the entire endeavor. When it comes to digitalization, the concept of a software platform such as zenon includes, by default, a wide range of key capabilities. A high level of connectivity to data sources and consumers is essential. Processing production data means implementing configurable information flows that are integrated within the overall OT / IT architecture. They fulfill the growing demands for solution performance. Dealing with increasing amounts of data challenges solution integration, too. Automated engineering is zenon’s specialty. It helps engineers to reduce their effort and time dramatically, while increasing solution robustness.
From prototyping to solution rollout, the software platform enables the project team to pick up the necessary building blocks and shape them with freedom and creativity, step by step.
Further transformation drivers
Digitalization represents a key driver of transformation in the Food & Beverage industry. However, it is not the only one. Our experience shows that current global challenges are testing the innovation capabilities of all industry players. How can manufacturers deal with changes to consumers preferences, logistical difficulties or even the growing skills gap? The best answers are delivered by following an overall vision of innovation. This vision might be for new products or packaging, improved processes or disruptive business models. Our real-life example of a business using zenon to empower people for process innovation and improvement, even while grappling with product diversification is a must-see video – and it’s just a mouse click away.
Sustainability sits alongside these other issues as part of our collective mission to beat global warming. The Food & Beverage industry is already addressing many aspects of sustainability, from optimizing energy consumption, to choosing new ingredients, creating a circular economy, and using renewable energy sources. The ideal situation is to integrate innovation and digitalization within your mission towards sustainability. Would you like to see how another customer of ours has managed to create a transparent production environment for carbon-neutral manufacturing? Read about it and watch the story here.
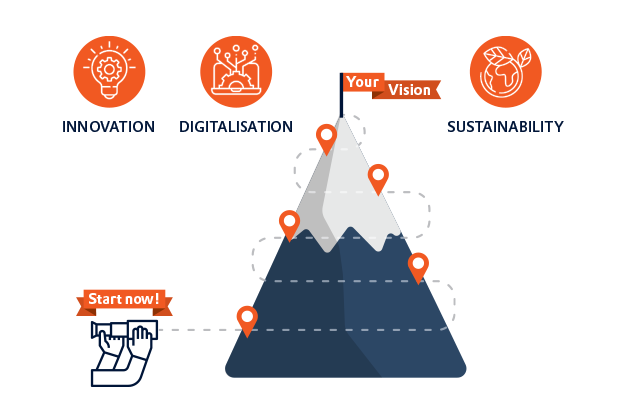
Transformation towards your vision can be shown as a journey towards the peak of a mountain. You may not reach the summit, but each step of the ascent is very important.
What are your newest challenges? How can we accelerate your ascent of the transformation mountain? How can zenon help you in the different areas of your manufacturing plant?
Making your life easier is our mission, together with our partner community and local representatives around the world.
I invite you to contact us, so we talk together.
Simply drop me an e-mail or find me on LinkedIn.
Are you also interested in part I and part III of this series? Please find them here:
Optimizing packaging processes – from pilot to rollout (part I)
Targeting CO2 neutrality (part III)