Wir befinden uns im Zeitalter von Künstlicher Intelligenz und ChatGPT, aber wenn Sie einen Blick in eine pharmazeutische Produktionsanlage werfen, werden Sie wahrscheinlich ältere Maschinen finden. Diese Maschinen mögen noch optimal funktionieren und wertvolle Daten erzeugen, aber sie sind oft nicht mit den IT-Systemen der Anlage verbunden. Ohne diese Konnektivität, die für genaue elektronische Chargenprotokolle (electronic batch record, EBR) unerlässlich ist, wird die Gewährleistung der Datenintegrität kostspielig und komplex. Die Integration von Bestandsmaschinen in die IT-Architektur eines Pharmaunternehmens kann jedoch eine Herausforderung darstellen.
Warum Bestandsequipment für die Datenintegrität kritisch ist
Die Einhaltung von Vorschriften hat für Pharmahersteller höchste Priorität. Bei Unternehmen, die Medikamente für den US-Markt herstellen, führen Mängel bei der Datenintegrität zu Verwarnungen durch die FDA. In Europa sind die entsprechenden Disziplinarverfahren die in der EudraGMDP-Datenbank veröffentlichten Non-Compliance Reports. Unternehmen, die ihre Probleme mit der Datenintegrität nicht beheben, müssen mit Geldstrafen oder sogar strafrechtlicher Verfolgung rechnen, was zu Rufschädigung führen kann.
Um die Datenintegrität zu gewährleisten, müssen Unternehmen genaue Chargenprotokolle führen, die detaillierte Informationen zur Produktionsqualität und Rückverfolgbarkeit enthalten. Bis vor kurzem wurden diese Aufzeichnungen überwiegend in Papierform geführt. Die jüngsten Vorschriften zur Datenintegrität zwingen die Unternehmen nun jedoch dazu, auf EBR umzustellen, die in der Regel auf einem Manufacturing-Execution-System (MES) basieren, um die Genauigkeit und Rückverfolgbarkeit zu maximieren.
Trotz des sich ändernden Rechtsrahmens ergab eine kürzlich durchgeführte Umfrage, dass etwa sieben von zehn Pharmaunternehmen immer noch papierbasierte Aufzeichnungen verwenden. Das Haupthindernis für die Umstellung auf MES-basierte EBR sind die hohen Kosten für die Integration und Validierung von Bestandsanlagen aufgrund der begrenzten Interoperabilität. Diese Datenprobleme sind häufig auf unzureichende Datenintegrationsspezifikationen zurückzuführen.
Herausforderungen bei der Datenintegration
Wenn Pharmaunternehmen Anlagen kaufen, stellen sie oft Leistung, Qualität und Sicherheit über die Datenintegration und Interoperabilität. Daher kann es passieren, dass diese Unternehmen versehentlich Maschinen kaufen, die nicht mit dem MES des Pharmabetriebs kompatibel sind. Das Ergebnis ist ein komplexerer Betrieb und höhere Integrations- und Validierungskosten, ganz zu schweigen von den Problemen der Datenintegrität.
Wenn die Maschine nicht mit dem MES kommunizieren kann, greifen die Bediener häufig auf den Manufacturing Equipment Monitor (MEM) zurück, um die letzten Meter zu überbrücken: "Papier-auf-Glas"-Ansatz. Diese Methode macht zwar papierbasierte Prozesse überflüssig, aber die Bediener übertragen die Daten immer noch manuell von einem HMI in ein anderes. Daher löst dieser Ansatz die mit papierbasierten Chargenprotokollen verbundenen Probleme der Datenintegrität nicht vollständig. Außerdem können wir ohne eine direkte Integration zwischen Fertigungslinien und MES das "Review by Exception" (RbE) nicht umsetzen, das für eine schnellere Chargenfreigabe entscheidend ist.
Integration von Greenfield- und Brownfield-Anlagen
Mehrere Branchenverbände haben Initiativen ergriffen, um herstellerunabhängige Datenintegrationsarchitekturen in der biowissenschaftlichen Produktion zu fördern. Dies ist eine gute Nachricht für neue Maschinen – die "grüne Wiese" (Greenfield). Diese Initiativen lösen jedoch nicht das Problem der Integration von "Brownfield"-Bestandsanlagen. Diese Einschränkung erfordert einen neuen modularen Ansatz für die Integration.
Ein typisches pharmazeutisches Produktionsunternehmen betreibt mehrere Softwareplattformen, die Daten in das übergeordnete Enterprise Resource Planning (ERP) einspeisen, um Compliance und Prozessoptimierung zu gewährleisten. Neben MES und HISTORIAN, die typischerweise in GMP-bezogene Funktionen eingebunden sind, umfassen andere Plattformen das Energiedatenmanagement (EDMS) und die Gesamtanlageneffektivität (OEE). Alle diese Systeme müssen nahtlos mit der Hardware der Produktionsanlage verbunden werden.
Ein typisches Brownfield-Szenario umfasst mehrere Maschinen von verschiedenen Herstellern mit unterschiedlichen SPS und SCADA-Systemen. Die Schnittstellen dieser Maschinen können je nach Art der Daten variieren – zum Beispiel können Zeitreihendaten auf OPC UA laufen, während andere Aufzeichnungen wie Audit Trails oder Alarmhistorie auf CSV-/XML-Dateien oder SQL-Datenbanken aufzeichnen. Eine weitere Herausforderung ist das Maschinenrezeptmanagement. Mit anderen Worten: eine typische pharmazeutische Produktionslinie hat mehrere kundenspezifische Schnittstellen, die schwer zu integrieren sind.
Die wichtigsten Schritte für eine erfolgreichen Automation Integration Layer
Der beste Ansatz, um die Komplexität der Datenintegration in Brownfield-Anwendungen zu überwinden, besteht darin, eine Middleware zwischen OT und IT zu schaffen. Dies wird als Automation Integration Layer (AIL) bezeichnet. Dieses System kann Daten kontextualisieren und aggregieren und gleichzeitig eine Zwei-Wege-Kommunikation zwischen jeder Maschine, ob alt oder neu, und den Softwareplattformen ermöglichen.
Aber wie können Pharmahersteller eine AIL effektiv implementieren? Der erste Schritt ist die Einführung von "Low-Code-/No-Code"-Softwareplattformen. Dieser Ansatz ermöglicht es den Anwendern, eine erweiterte Konnektivität mit Maschinen und Anlagen verschiedener Hersteller zu erreichen, auch mit älteren Maschinen, ohne für jede Maschine einen eigenen Code schreiben zu müssen. So bietet die Software zenon beispielsweise über 300 Optionen, die eine Verbindung mit praktisch jeder Hardware ermöglichen, die sofort einsatzbereit ist.
Der zweite Schritt ist die Anwendung der modularen Technik auf Software und Hardware. Mit Plattformen wie zenon können Betreiber ein Datenintegrationskonzept für eine bestimmte Maschine erstellen, das einfach auf andere Maschinen derselben Kategorie übertragen werden kann, um so eine zentrale Softwarebibliothek für Maschinen aufzubauen. Dieses Konzept ermöglicht es den Herstellern auch, neue Anlagen nahtlos zu erweitern und zu integrieren, wenn sie die Produktion ausweiten müssen.
Der gleiche modulare Ansatz gilt auch für die Hardware. Edge-Komponenten in der Nähe der Maschinen sind unerlässlich, um die Datenintegration und die Zwei-Wege-Kommunikation mit dem IT-System zu gewährleisten, wobei die Daten sicher vom Fertigungsbereich in die Cloud übertragen werden.
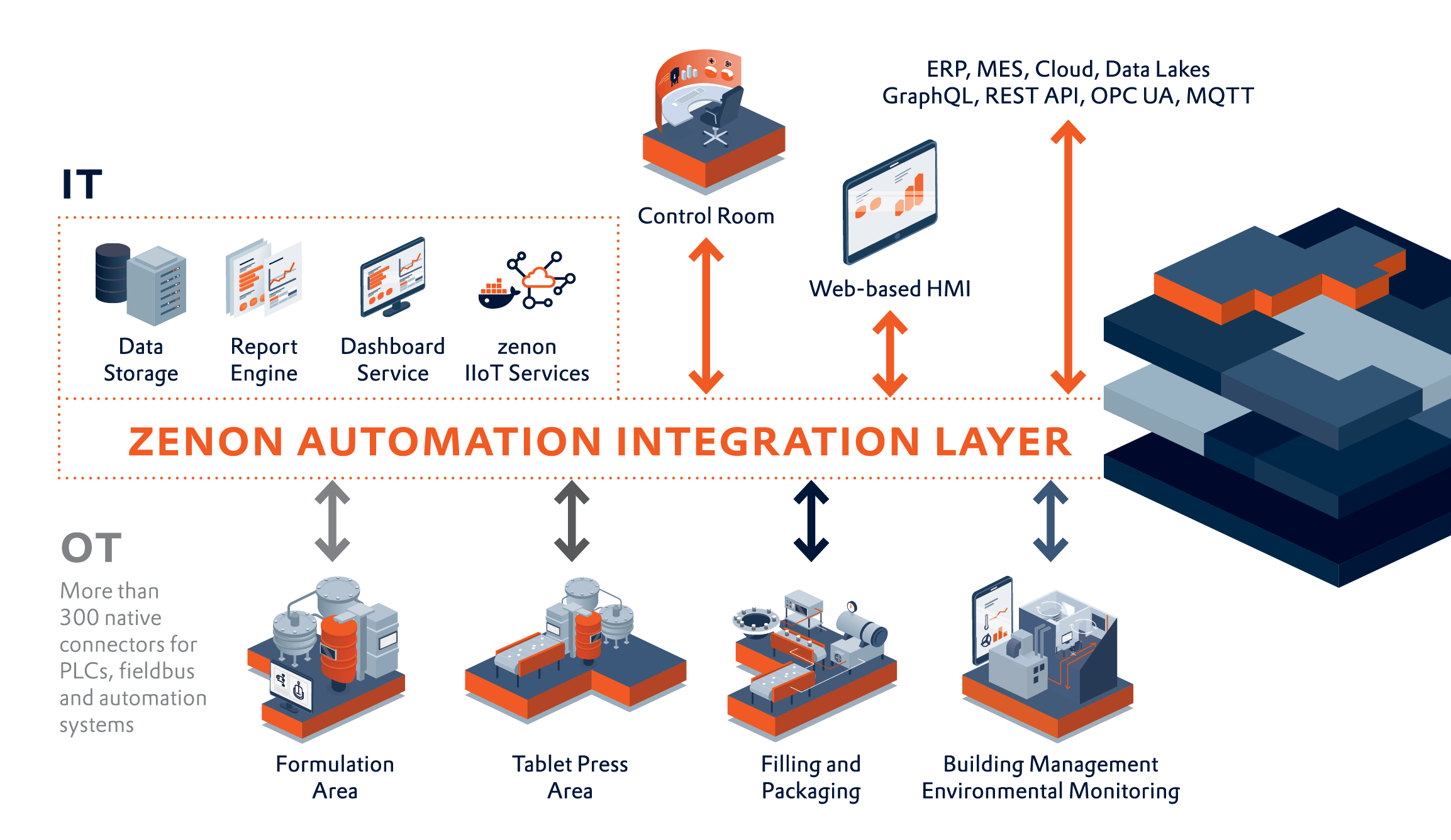
Die Kombination aus skalierbaren Hardware-Lösungen und Software-Bibliotheken ermöglicht es Pharmaherstellern, Maschinen schneller und kostengünstiger zu integrieren. Ein modularer Ansatz, der auf einem AIL basiert, kann auch großen multinationalen Organisationen zugute kommen, die dieselben Softwarebibliotheken an verschiedenen Standorten in unterschiedlichen Ländern nutzen können.
Die Zukunft ist modular
Ein modularer, auf einem AIL basierender Entwicklungsansatz kann Pharmaherstellern über die Datenintegrität hinaus Vorteile bringen. Durch die einfache Datenintegration und erweiterte Konnektivität können Unternehmen die Effizienz- und Produktivitätsgewinne realisieren, die neue Technologien wie KI ermöglichen.
Bessere Datenintegrität führt zu höherer Produktivität dank schnellerer Chargenfreigaben. Ein AIL-Ansatz trägt auch zur Demokratisierung von Daten bei, da Teams im gesamten Unternehmen auf Daten zugreifen und diese analysieren können, um Prozesse, Qualität und Effizienz kontinuierlich zu verbessern. Mit einem AIL können Pharmahersteller sicherstellen, dass alle Maschinen, einschließlich älterer und neuer, eine Rolle bei dieser Transformation spielen.
Lesen Sie auch unseren englischen Originaltext How to integrate legacy equipment’s data in pharma.